4 inch butterfly valve
spring loaded ball valve
2 inch valve
The end-user, Jiahua Energy Chemical Industry Co, is a kind energy and chemical group that was invested in a continuous sulfur trioxide sulfonation (waste acid cracking) project to realize the recycling of sulfur resources by introducing the waste acid cracking process technology from MECS Inc in 2020.
How to Choose Valves For the Chemical Industry
Chemical Industry – Case Study
THINKTANK, as a professional valve manufacturer, was participate to supply chemical valves for this project. Pneumatic diaphragm globe type control valves, pneumatic ball valves, and pneumatic eccentric butterfly valves are THINKTANK’s main products and we feel so proud to have completed the delivery of the sulfur trioxide continuous sulfonation (waste acid cracking) project on time. It includes pneumatic single-seat control valves, pneumatic cage type control valves, fluorine lined control valves, bellows control valves, low noise control valves, self-operated pressure regulators, and other different kinds of pneumatic valves totaling more than 100 units.
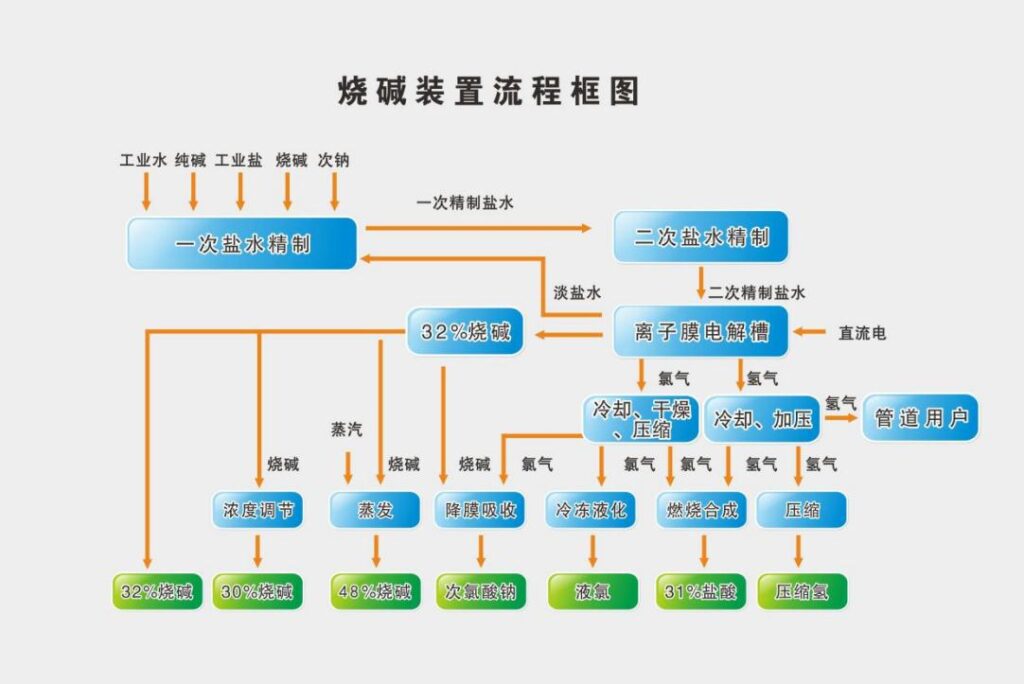
Chemical Products
① Chlor-alkali products
Jiahua Energy caustic soda products mainly include the following specifications: 30% caustic soda, 32% caustic soda, 48% caustic soda, sodium hypochlorite, liquid chlorine, 31% industrial hydrochloric acid, 31% high purity hydrochloric acid, and hydrogen gas.
The main alkali production processes are the ion membrane method, diaphragm method, and mercury method. The ion membrane method of caustic soda has the advantages of low energy consumption, low pollution (no mercury, lead, asbestos, and other pollution), and high product purity, which is the most advanced alkali production technology in the world at present. As an advanced technology for caustic soda production As the advanced technology of caustic soda production, with its low energy consumption, low emission of three wastes, high degree of operation automation and safety, low cost, and other outstanding It is the most used technology in China’s caustic soda industry at present. At present, Jiahua Energy has two sets of ion membrane caustic soda plants with a total scale of 297,000 tons.
② Fatty alcohol (acid) products
The overall process is to first hydrolyze the fatty acid, then methyl ester reaction to produce fatty acid methyl ester, fatty acid methyl ester using low pressure gas phase hydrogenation process, under the action of catalyst, hydrocracking to fatty alcohol and methanol, methanol recycling. The fatty acid methyl ester is produced by low-pressure gas-phase hydrogenation process and hydrocracked into fatty alcohol and methanol under the action of a catalyst, and the methanol is recycled and reused. The fatty alcohols are refined to obtain fatty alcohols.
③ Sulfuric acid products
Jiahua Energy’s sulfuric acid products mainly include the following specifications: 98% industrial sulfuric acid, fuming sulfuric acid, liquid sulfur trioxide, AR grade sulfuric acid, and chlorosulfuric acid. Chlorosulfuric acid.
Liquid sulfur is atomized and burned in the sulfur incinerator to produce SO2, and the resulting high temperature process gas is recovered by the waste heat boiler to produce medium pressure saturated steam. After the process gas is cooled, it enters the second section of the reformer, where the remaining SO2 continues to be converted to SO3 and gives off heat. In the first absorption tower and in the fuming acid absorption tower, the product sulfuric acid and fuming sulfuric acid are produced. The process gas passing through the first absorption tower enters the fourth section of the converter, which finally converts more than 99.5% of SO2 into SO3, cools down, and enters the second absorption tower, which absorbs the SO3 and produces sulfuric acid, and the exhaust gas is further absorbed and treated by the power wave unit and exhausted through the chimney.
The fuming sulfuric acid is heated and evaporated by the evaporator to produce gas sulfur trioxide, and the gas sulfur trioxide is divided into three ways, one way is condensed into liquid sulfur trioxide by the condenser, and the liquid sulfur trioxide is sent to the user through the pipeline; the other way is sent to the chlorosulfuric acid system; the third way is sent to the AR acid absorption tower to produce refined sulfuric acid and AR grade sulfuric acid. The hydrogen chloride gas from the 31% hydrochloric acid desorption is freeze-dried and fed into the chlorosulfonic acid synthesis tower, where the hydrogen chloride and sulfur oxide react to form chlorosulfonic acid.
④ Sulfonated pharmaceutical products
The production of o-toluene sulfonyl chloride adopts the patented technology of continuous sulfonation reaction of liquid sulfur trioxide and toluene developed by the company, which is at the domestic advanced level of the industrial production process of this series of products.
The process changes the production technology of intermittent sulfonation of excess chlorosulfonic acid and toluene, which has been used for many years, and adopts the new environmental protection technology of continuous sulfonation of liquid sulfur trioxide and toluene, and then produces o/p-toluene sulfonyl chloride through continuous chlorination and continuous crystallization and separation, and this process can produce more than 95% of a p-toluene sulfonyl chloride with large market capacity.
In the energy chemical project, because the process parameters are complex, process selection requirements are extremely high, our technical staff and site engineers have been in constant communication, from flow capacity to chemical valve sizing, we constantly improve the technical solutions, and finally successfully use the site and perfect completion of the commissioning. More than 60 sets of pneumatic fluorine-lined butterfly valves, ball valves, and triple eccentric butterfly valves were also installed and commissioned at the end of May.
Control Valves 101: Valve Types, Applications, Components, and Accessories
The Applications for Chemical Products
Products | Industry Catagory | Main Upstream Raw Materials | Main Downstream Applications |
Fatty alcohols (acids) | Grease Industry | Palm kernel oil | Daily chemical industry |
Sulfonated pharmaceutical products series | Organic chemical product system | Toluene, chlorosulfonic acid | Pharmaceutical intermediates, dyestuff chemicals etc. |
Chlor-alkali | Chlor-alkali industry | Salt | Printing and dyeing, chemical fiber, fine chemical |
Sulfuric acid | Inorganic chemical | Sulfur | Fertilizer, chemical |
Various Chemical Valves
Pneumatic Diaphragm Globe Type Control Valves
Pneumatic diaphragm globe type control valves are the most important control element in the chemical processing, they received the input signal of the automatic control system to modulate flow capacity, downstream pressure, and temperature data. Pneumatic diaphragm globe type control valves have the advantages of fast response, simple operation, safety, and reliable performance.
What is the difference between v-port ball valves and globe control valves?
Pneumatic Ball Valves
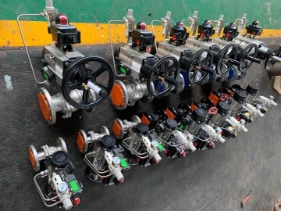
Pneumatic ball valves are very commonly used for on/off or shut off application, it has tight close with short time, with the fastest switching speed of 0.05 seconds/time. Pneumatic ball valves assemble with various accessories, such as solenoid valves, air filter regulators, limit switches, handwheel operators, boosters, etc., in order to achieve local control and remote centralized control. Pneumatic ball valve specific classification are pneumatic stainless steel ball valve, pneumatic plastic ball valve, pneumatic sanitary ball valve, pneumatic carbon steel ball valve, pneumatic two-way ball valve, pneumatic three-way ball valve, pneumatic four-way ball valve.
Pneumatic Eccentric Butterfly Valves
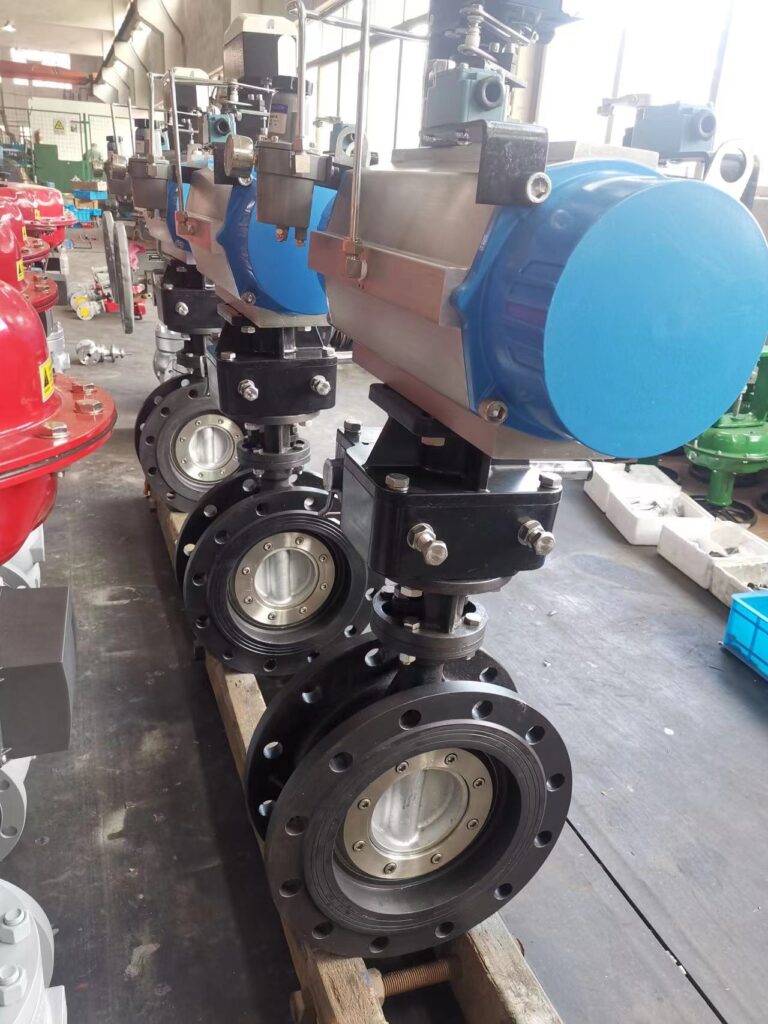
How to Find a Reliable Triple Eccentric Butterfly Valve Supplier in China?
Pneumatic eccentric butterfly valves are high performance valves with cost-effective for control applications, compare with globe type linear control valves the costs are lower. For large flow capacity, we recommend using butterfly valves.
Pneumatic Cage Type Control Valves
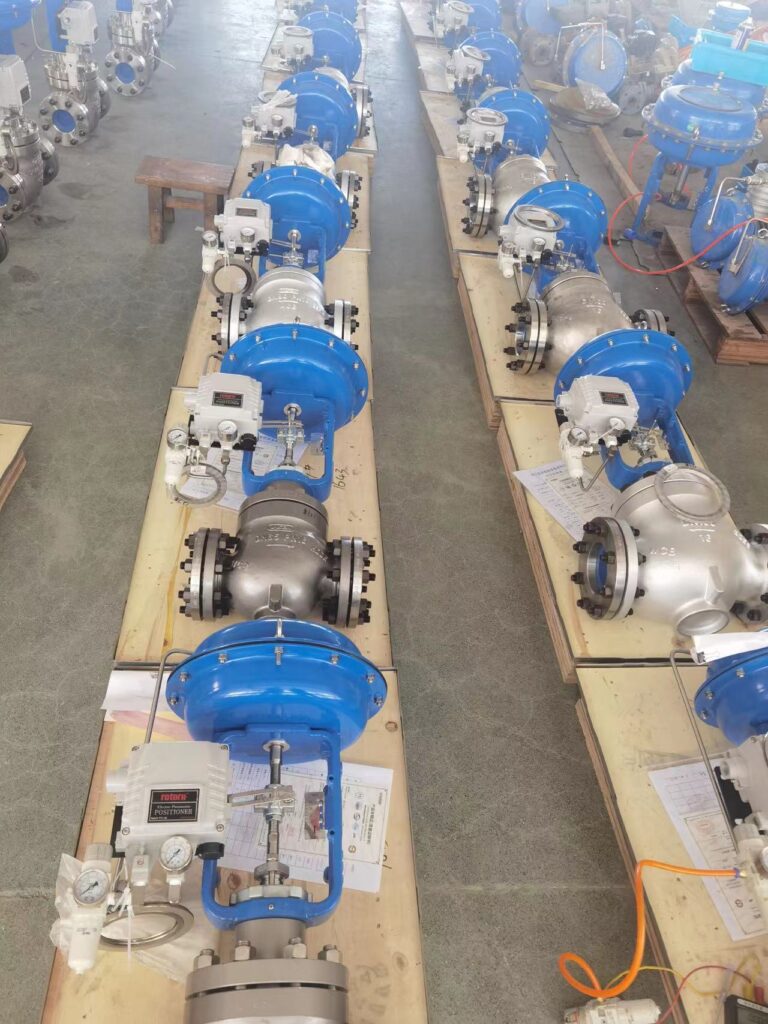
Pneumatic Fluorine Lined Control Valves
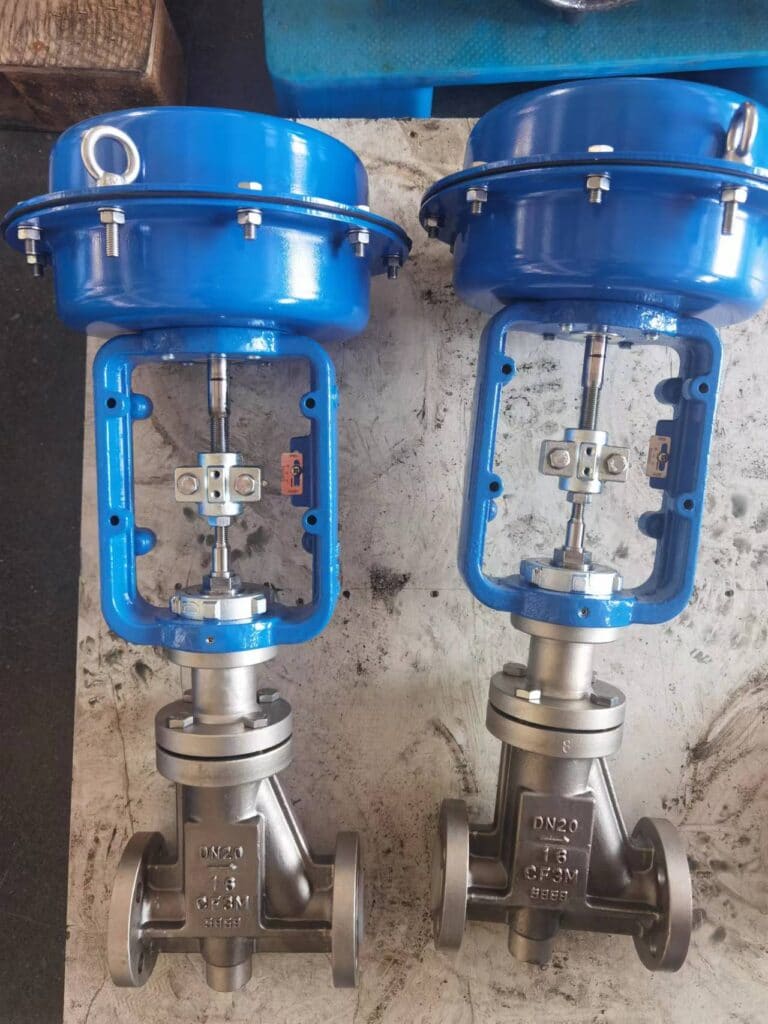
Pneumatic PTFE lined control valve is composed of two parts: pneumatic actuator and fluorine lined valve body. The design of internal parts completely lined with fluorine effectively blocks the corrosion of corrosive media to the metal material in the valve. The inner cavity of the metal valve body adopts special technology to make the lining material completely join with the metal and prolong the service life and performance of the lining material. The valve stem seal can be sealed by a combination of the F46 bellows seal and PTFE packing, completely eliminating the possibility of media leakage from the stem to the outside. The unbalanced fully lined structure is specially designed for use with very corrosive media under low pressure ambient temperature conditions.
The parts of the pneumatic PTFE-lined control valve body in contact with corrosive media are made of corrosion-resistant, anti-aging polytetrafluoroethylene propylene, high-pressure fluorine plastic lining process, and polytetrafluoroethylene bellows seal. The PTFE-lined pneumatic control valve has the regulation of the flow of acid, alkali, and other highly corrosive media and toxic volatile gas and liquid media. Therefore, the Teflon-lined pneumatic control valve is widely used in chemical, metallurgical, pharmaceutical, and other industries. The main characteristics of the product.
1.Good corrosion resistance
The valve body cavity, plug, and seat, all are lined with 3mm thick PTFE, which can resist strong corrosive fluids.
2. Good sealing performance
Teflon bellows and packing double sealing.
3. Less leakage
The leakage of the plug and seat is soft seal is much lower than the ANSI Class IV standard.
4. High control precision
The pneumatic PTFE-lined control valves have a compact design, and the control precision could achieve at 0.5%.
Pneumatic Globe Valves
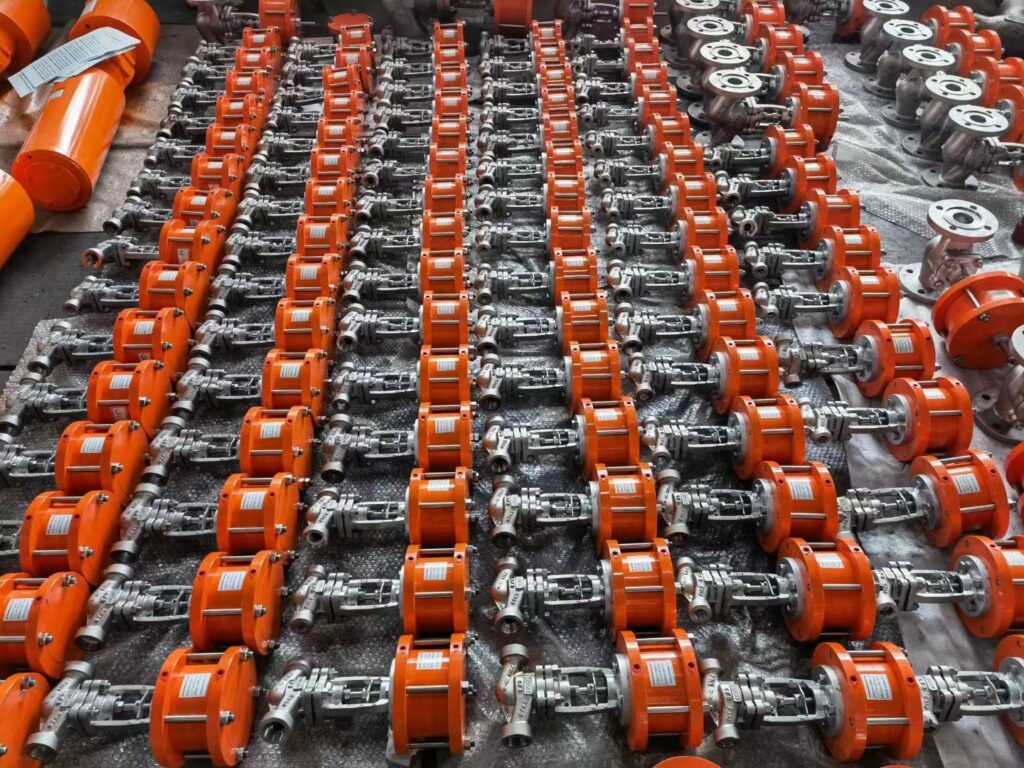
The pneumatic globe valve is a widely used valve type in chemical plants. Its sealing performance is reliable, and also suitable for regulating the flow, generally installed in the pump outlet, control valve bypass, flowmeter upstream and other places where the flow needs to be adjusted.
Low Noise Control Valves
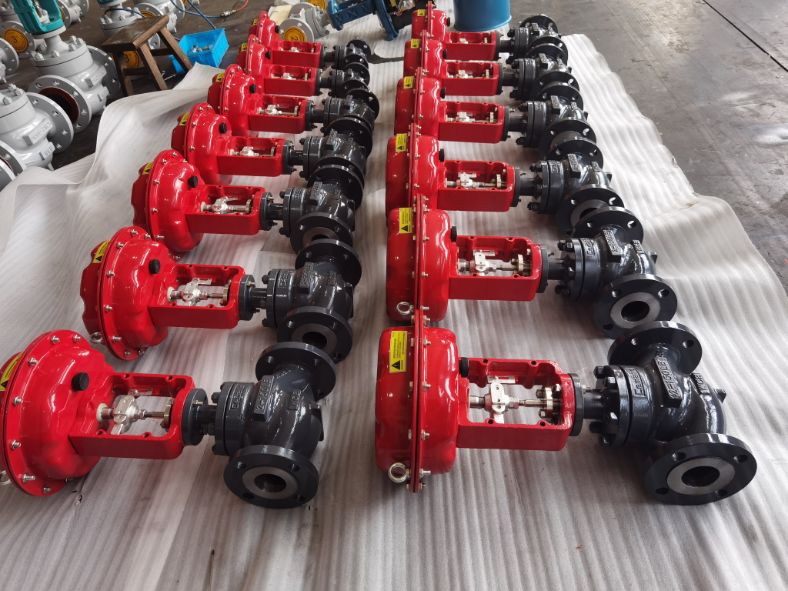
Low noise control valves are multi-stage cage or labyrinth type, multi-stage decompression, complete control of the flow of the medium through the valve, significantly reducing the noise generated by high-pressure gas or steam in the valve. A stable multi-stage pressure reduction design effectively makes the liquid not produce cavitation, especially suitable for use in high-pressure media applications.
This control valve is mainly suitable for large differential pressure, working conditions produce flash, cavitation occasions. According to the different parameters of the design of a number of different pressure-reducing cages, to form a multi-stage pressure-reducing internal part to ensure the elimination of the valve flash and cavitation phenomenon. Media from contact with the first cage to start throttling, through multiple throttling will be the inlet of the high-pressure difference gradually reduced, so as to effectively ensure that the medium in the valve flow, the pressure is always above its saturation vapor pressure, also eliminates the possibility of flash, cavitation phenomenon, extending the service life of the valve in harsh conditions.
Self-operated Pressure Regulators
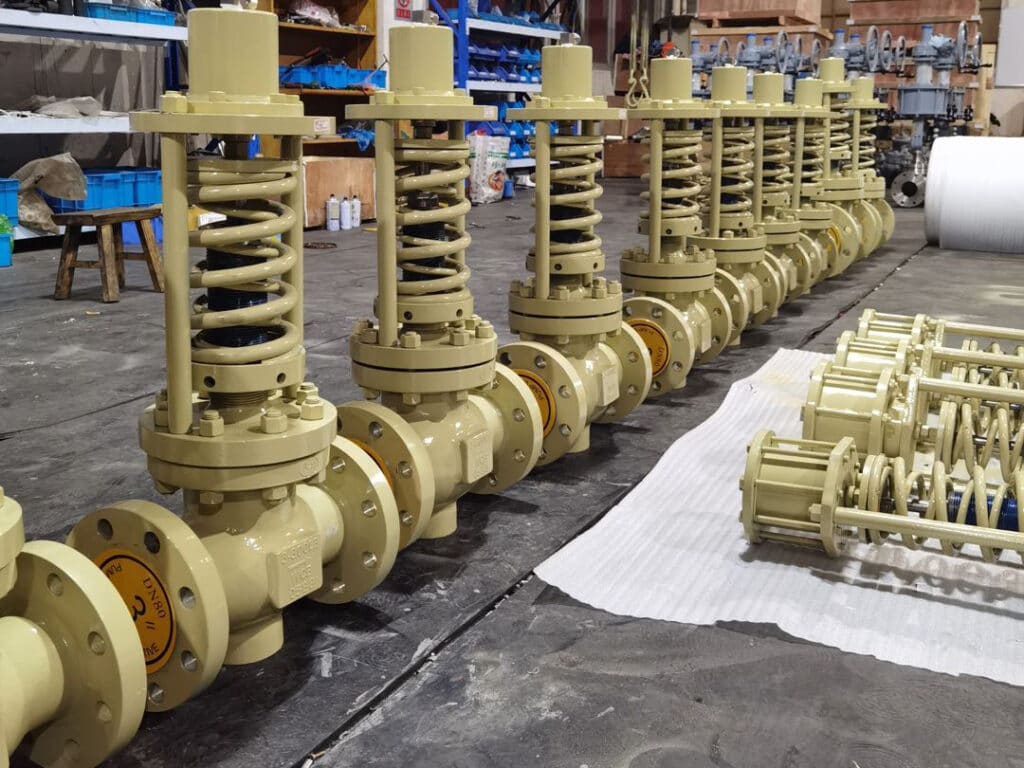
The self-operated pressure regulators use a modular design, which is easy to assemble and maintain, and significantly reduces costs. In addition, it no needs any power but drives by the fluid itself automatically. It can continue to operate in the event of a power failure, making it safer and more reliable.
THINKTANK has been continuously providing various solutions to achieve high-performance operation and save more costs for the owner at the same time. From valve factory to an engineering company to end-user, one-stop service is more effective, faster, and more cost-saving. Should you have any questions, welcome to send us your inquiry to marketing at cncontrolvalve.com.
How to quickly understand various industrial valve types and their applications?