8 butterfly valve dimensions
butterfly valve fire fighting
xomox butterfly valve
steam butterfly valve
While electrical and pneumatic actuators have several unique benefits and are preferred in different applications, using the wrong one for your application can have serious consequences. However, choosing between them can be quite confusing. This article explores the working principles and differences between pneumatic and electric actuators, before comparatively analyzing their features to help you choose the right one for your application.
Valve actuators are automation devices that are used to remotely control valves without human intervention. These devices generate motion to control valves based on signals received. Actuators are mounted on the valves to be controlled, replacing manual levers. The mounting features that connect a valve to an actuator vary in different actuator models.
Valve actuators are broadly classified based on how they generate the torque – or force – required to open a valve. Based on this classification, the two most prevalent types of actuators are electric and pneumatic actuators. Electric valve actuators utilize electricity to produce the required motion, while their pneumatic counterparts utilize compressed air systems. The third type of valve actuator, known as hydraulic actuators exist, but these are less prevalent.
Electric actuators
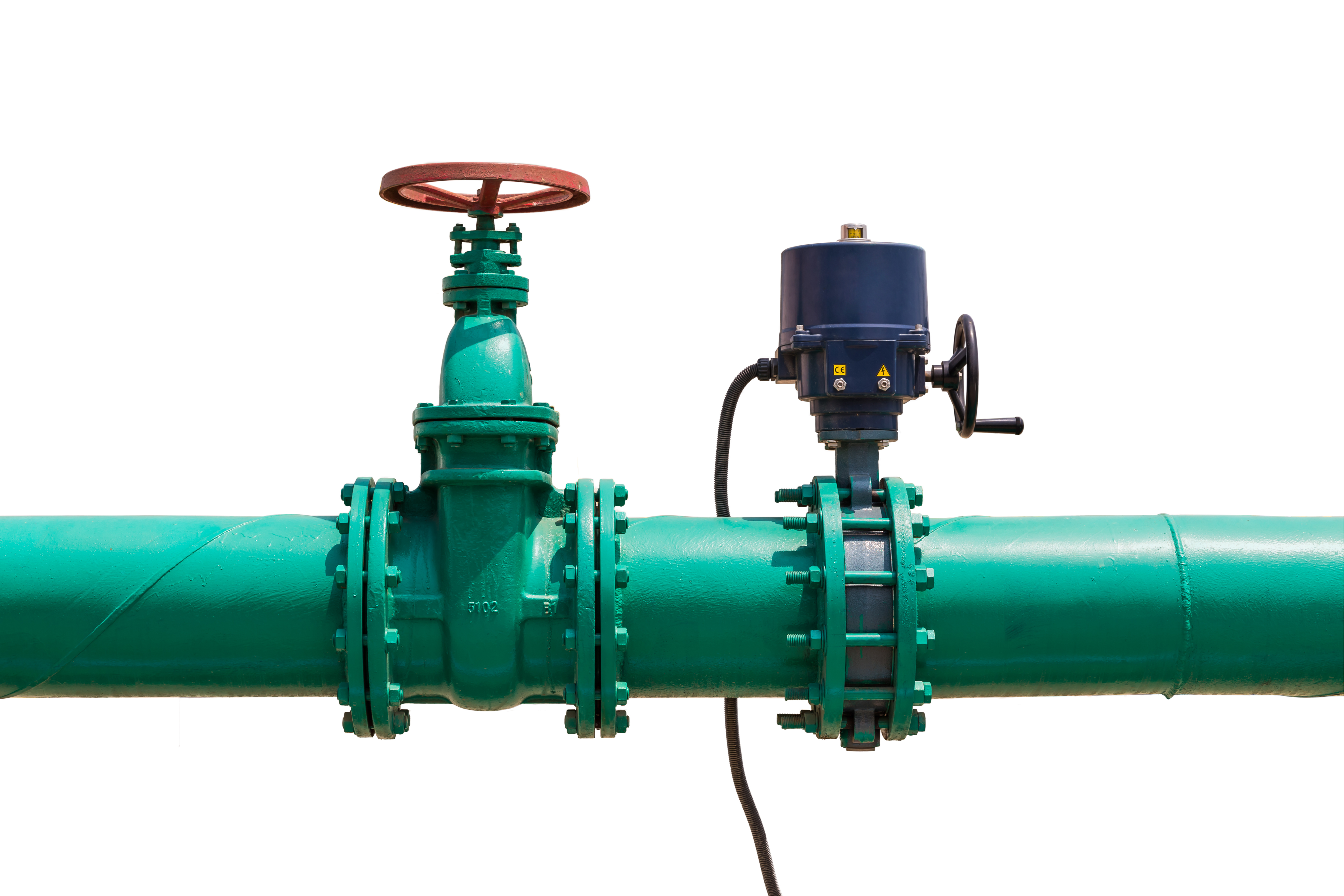
Electric actuators convert electrical energy into the force that opens or closes the valve. These devices may run on AC or DC power. Electric valve actuators may feature an electric motor that produces the rotary motion that turns the valve. This type of actuator is used for quarter-turn valves, which require a 90° turn to open or close, and are known as quarter turn actuators. Examples of quarter-turn actuators are ball and butterfly valve actuators.
Another widely used type of electric actuator in piping and fluid control systems is the solenoid actuator. These devices are typically available integrated with the valves, forming a single unit.
Pneumatic actuators
Pneumatic actuator utilizes pneumatics – controlled compressed air systems – to produce the force required to operate a valve. These actuators may feature a piston, or diaphragm, that is controlled via compressed air. The more ubiquitous piston-featuring variety contains a piston housed in a chamber. Pneumatic actuators may be single-acting or double-acting. Single-acting actuators, more commonly known as spring return actuators, feature a loaded spring on one side of the piston that keeps the valve in its natural position. To open or close the valve, pressurized air is supplied on the other side of the piston, and the air pressure overcomes the force of the spring.
On the other hand, in double-acting actuators, the air is supplied to both sides of the piston. The difference in pressure between the two sides keeps the valve in the desired position. Pneumatic actuators typically produce linear motion. However, in actuators such as butterfly valve actuators (which are required to generate rotary motion), motion conversion mechanisms – such as rack and pinion, and scotch yoke mechanisms – are used.

Choosing between an electric and a pneumatic actuator
Both electric and pneumatic valve actuators have specific advantages in different applications. To choose the right one for your application, certain factors and characteristics of these actuators have to be analyzed. Some of these factors and characteristics are explored below.
1. Precision
Precision is considered for valves that need to operate in partially open or closed positions to allow an exact amount of media to flow through. Both electric and pneumatic actuators provide precise control. However, when relying on pneumatic actuation, the inclusion of an electro-pneumatic positioner may be required as an accessory on a pneumatically operated device such as a control valve to achieve the high precision control necessary in applications such as chemical production.
2. Force range
Pneumatic actuators provide a significantly higher force/torque per unit side than their electric counterparts. For applications that involve a large valve or a valve with high operating pressure, pneumatic actuators are the better option.
3. Speed
Speed of actuation is a crucial consideration in specific applications such as flood control. Like with precision, both electric and pneumatic actuators can be fast. However, a pneumatic actuator reacts faster and has high duty cycles. Furthermore, the operating speeds of pneumatic actuators are adjustable.
4. Lifespan
Pneumatic actuators have fewer components. Therefore, they are easier to maintain and have a longer lifespan than electrical actuators, which have several parts that may require regular maintenance. However, while the actuator unit may not require maintenance, other components such as the air compressor and the FRL (Filter, Regulator, and lubricator) may require more frequent maintenance
5. Cost
The design of pneumatic valve actuators is more straightforward than that of their electric counterparts, and so these actuators cost less than electric counterparts. However, when the cost of the accompanying pneumatic system is considered, the overall cost of a pneumatic actuation system increases. This cost can be significantly reduced by setting up numerous actuators with the same pressurized air supply system.
6. Fail safe
In applications where a failure in the actuator can have severe consequences, the actuator needs to have a fail-safe mechanism. A fail-safe is easier and cheaper to install in pneumatic actuators. Spring return pneumatic valve actuators feature a natural fail-safe mechanism, as the force of the spring will automatically return the valve to its natural position in the case of a failure.
7. Hazardous conditions
Electric actuators often feature delicate components that may not function correctly in hazardous conditions. Furthermore, these actuators require numerous certifications in order to be deemed suitable in certain environments. Electric actuators need a high level of protection against high temperatures and pressures, dust, and moisture. On the other hand, pneumatic actuators are quite rugged and can withstand higher pressures and temperatures than their electric counterparts.
Conclusion
Both pneumatic and electric actuators are efficient and highly functional automation devices that are employed across various industries. However, they each possess unique characteristics that make them preferable in different applications. To select the best one for your application, carefully consider the above-listed factors.
Need guidance in determining the appropriate valve actuator for a specific application?
The experts at ValveMan have the knowledge and experience to help. Shop ValveMan.com today!
Related Products
[[2220, 1438, 116]]